Safety and Reliability
Starzen Group Quality Policy
In accordance with our management philosophy “Connecting people and food around the world through inspirational experiences”, the Starzen Group has established a “Quality Policy” to further improve the quality of our products and satisfy our customers.
The Starzen Group is sincerely committed to providing safe,
secure and healthy food,
and aims to make people smile.
Our Promise to Customers
The Starzen Group will earnestly listen to customers, work to develop products and improve our services, and strive to provide better products.
Legal and Regulatory Compliance
The Starzen Group complies with all food-related laws and regulatory requirements, and acts in accordance with internal rules and regulations.
Quality Assurance Activities
All employees of the Starzen Group are committed to making safe and secure products by responsibly managing each process from production to sales so that we can provide high-quality products without waste and with respect for precious lives.
Vision for Our Human Resources
All employees of the Starzen Group proactively work to improve their knowledge, skills, and expertise in food safety and security, and to enhance each other’s knowledge and awareness, as the Starzen Group seeks to become a team of professionals who handle food products.
Safety and Hygiene Management Systems
Aiming to Provide Safe Products
For the Starzen Group, which believes in putting the customer first, we consider it our important
mission to provide safe foods that customers can rely on. Consequently, we established the Group
Quality Assurance Department to ensure that food hygiene inspection is thoroughly implemented. A
quality assurance officer is appointed at each business site, to check the hygiene management of the
facility, product labeling, and related matters.
For Japanese domestic beef and pork, we have created a production history information trace back
system to enable disclosure of the background of beef and pork to provide safe, reliable and
trustworthy products with assured quality.
Fastidious Approach to Taste and Quality
The Starzen Group prioritizes the manufacture of safe and reliable products in order to deliver products that are trusted by customers. To that end, we established the Quality Assurance Department as described above. To further enforce our policies, each plant follows the HACCP food sanitation management system, and employs strict safety control over all processes from the stage of selecting good quality raw ingredients to delivery to customers.
Safe Quality Food (SQF)
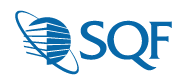
The Starzen Group’s Iwaki Sales Office was the first distribution business to acquire SQF
certification in Japan. and our Koriyama Plant was the first within our company to acquire it.
To date, 57 sites across the group, including 20 plants, have acquired the certification (As of April 1, 2025).
In brief, SQF is a system that secures the safety and quality of food. More specifically, it
establishes important quality points based on HACCP system to prevent safety and quality
hazards, ensuring thorough process control in food handling, thereby contributing to stability
in quality.
Starzen Group’s SQF
A First in Japan! Integrated Management from Production to Distribution Under SQF
SQF certification obtained at57Group locations within Japan
The Starzen Group has unified its external certifications under the SQF standard.
The integrated management structure we have built under SQF from production (farms) to distribution
(business locations) is a first in Japan.
-
We prepared a standardized manual and obtained approval of the SQF certification body for its
use.
→Eliminates variations in quality control knowledge, ensuring uniform quality control. -
We divided our business locations into multiple groups, and a representative location from
each
group undergoes the renewal assessment.
→Provides advantage of having business locations within each group work together on quality control.
SQF Initiatives
In order to acquire and retain SQF certification, it is imperative that safety and quality be
ensured in all processes related to receipt, storage, processing/manufacture, packaging,
transportation and shipment of products purchased and sold.
For this reason, we are engaged in the following efforts to maintain quality at each of our business
sites.
Receiving

Storage
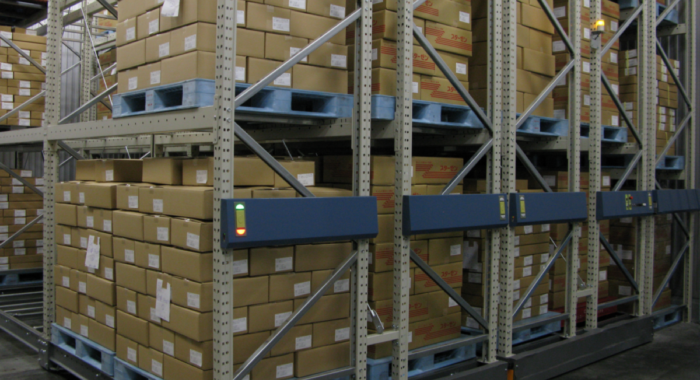
Processing and manufacturing
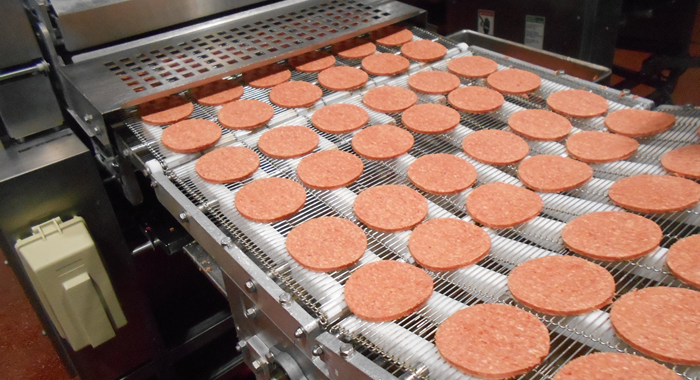
Packaging
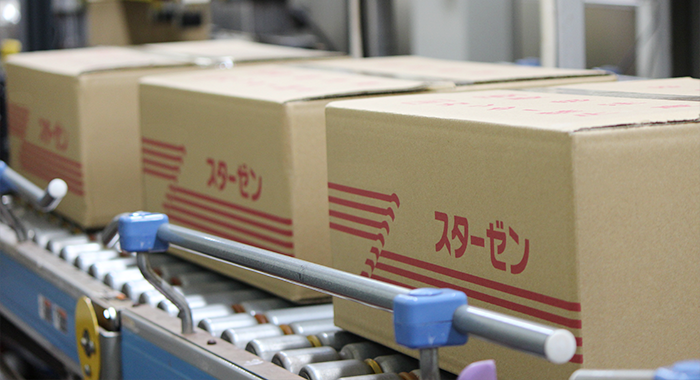
Shipment
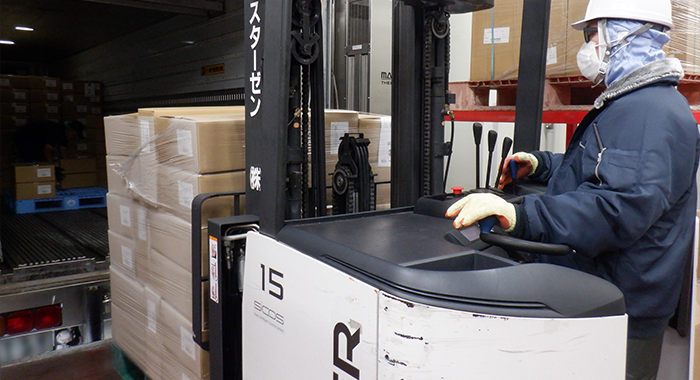
Hygiene management
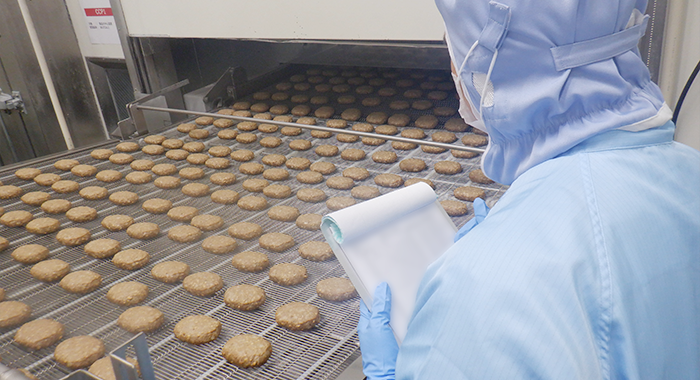
Inspection
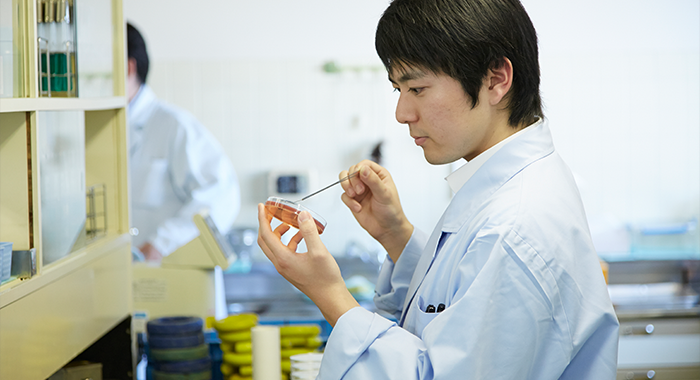
Traceability
Discloser of the production trace back information
Starzen Group established a system of production trace back information on domestic cattle, and in
February 2003, we started sharing this information, as one aspect of providing safe and reliable
products. This information includes personal information from producers obtained with their consent,
together with information provided by the National Livestock Breeding Center.
We also implemented this for Japanese pork from June 2004. Information regarding Japanese domestic
cattle was made accessible from certain cell phones from September 2003.